QUOTE (billy_ocean @ Dec 8 2008, 11:58 PM)

wow, what do you guys think about these little pins?
Somehow I missed this. The pins are probably hardened steel so they MIGHT be strong enough assuming they are short enough. But I completely agree with TB, they don't appear to be retained well.
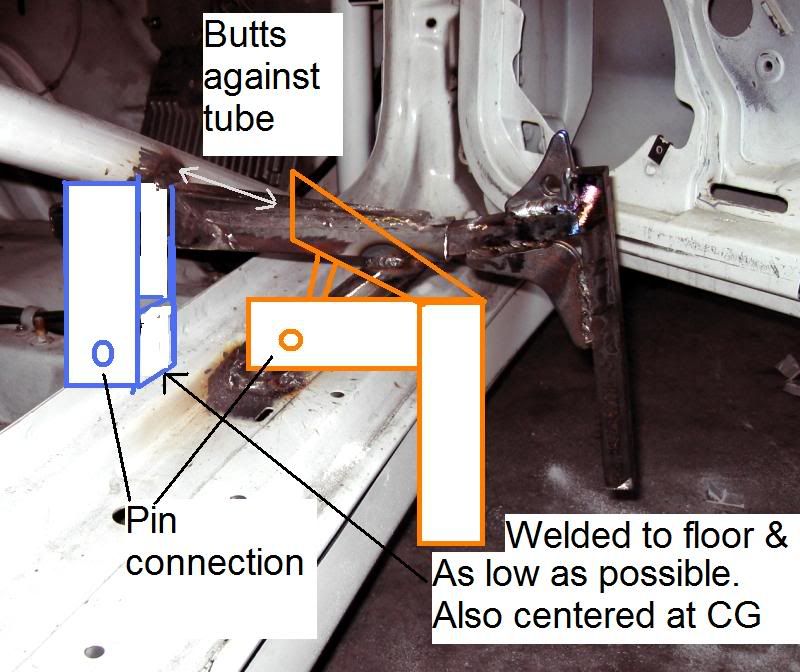
So, I've put some more thought into my contraption above I don't think it will work. Since the jacking point is ~6" out to the right to clear the rocker panel, the vertical bar that is tied between the rocker and the X will be resisting a bending moment i.e. the top will be getting pushed in (to the left) and the bottom will be getting pulled out (to the right). I think the top would be ok, but the rocker panel won't be strong enough since it is only sheet metal.
So here is a better idea:
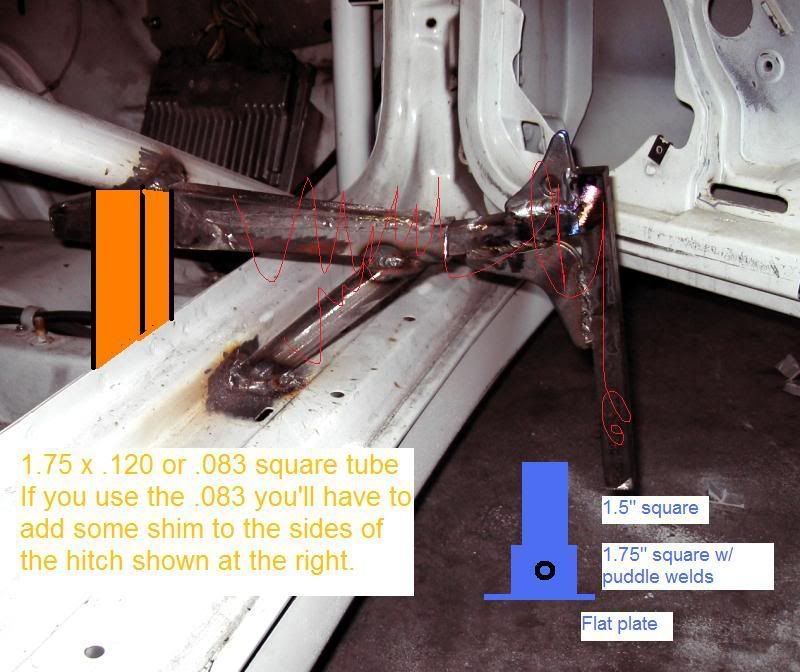
Cut a square hole in the floor so the square tube can pass through. Make the hole flush with the pinch weld in the rocker so it can be welded directly to the rocker. This takes away almost all of the bending loads caused by versions 1 and 2 and is the simplest solution for x-bars, I think.
You have a couple options for the bottom part where the jack would touch. You can either weld a plate to the bottom and call it good. Or you can make a separate "hitch" as shown in blue in the picture. The benefit of the separate piece would be ground clearance since I'm not sure if I like the idea have having a blunt object sticking out at the ground line.
This is so much simpler. Looking back I don't know why I didn't think of this first.
Hopefully it works since I've already hacked out my SFC's (which is a dirty dirty job BTW).