HoosierPE
Jun 19 2013, 07:23 PM
Greetings fellow F-body enthusiast!
I've created this new topic to introduce Hoosier Performance Engineering's first new product; a clean sheet approach to a billet front hub and bearing assembly for the 4th Gen F-bodies and C4 Corvettes. Many of the other hub/bearing threads are getting pretty long and don't really end with a sustainable solution, so I thought a new thread was in order.
I won't bore you with the details on HPE, other than to say a group of highly qualified and skilled automotive engineers have gotten together to create performance products for the 4th Gens and modern muscle cars. You can read more about HPE on the General Discussions forum where Kevin introduced HPE as a new sponsor.
I've been contemplating the 4th Gen front hub issues since I returned to Auto-X in the fall of '97 with the purchase of my first TA and began working in earnest on new designs in November of last year. What you see below is the result of two gear-heads' work for the past 7 or 8 months, plus over $6000 worth of invested in prototypes, tooling and CNC programming. Prototypes are installed and accumulating mileage and we will be ready to take orders as soon as the machine shop volume quotation is received and final pricing can is set. (Trying to wrap up pricing yet this week.)
I'll let the pictures do the talking first, and then will follow up with some detailed descriptions of the components. Enjoy.
Finished product:

,

Here's a disassembled OEM hub and the new HPE replacement parts. Note the OEM uses ball bearings while the other is tapered roller. On Timken's website, the tapered bearings are rated much higher in every category vs. the ball bearings. Small bearing has a 1.25" ID and the large bearing has an 1.5" ID. For comparison, the old GM RWD cars used like 7/8" and 1" bearings with the front spindle design.




We use an inverted spindle design, much like OEM part, except ours is a two piece design with a wheel mounting flange and pin (spindle) that we shrink fit together. The shrink fit provides three times the push out force of an equivalent press fit. Pin, flange and housing were all coated with a clear zinc treatment. The pin has been case hardened in the two areas where the bearing races will rest. The mounting flange is case hardened where the seal will run. Specs were per the Timken recommendations for the bearings used.

Pin with locking washer, nut and small cap screws. The washer engages the key way in the in threaded end of the pin, the nut is added and torqued to desired preload, and when the threaded holes in the nut lines up with the holes in the washer, the cap screws are added as the retention mechanism, basically replacing the cotter pin in similar parts.


Sub-assembly shown with dry bearings for clarity.

These assemblies are completely rebuildable and repackable. Should be the last set you will ever need.
I will add some more pictures of the prototypes installed on one of our cars.
Please let me know what you think!
Steve91T
Jun 19 2013, 07:38 PM
I would buy one just to put in a display case. The most beautiful car part I think I've ever seen.
Maybe I missed it, or maybe you aren't announcing it yet, but any idea how much they will cost? I would assume with any race specific part, there won't be a warranty, right?
00 SS
Jun 20 2013, 12:41 AM
Nice job. The two piece spindle and flange seems like a good idea. I can't wait to see how it holds up to 315 and AX abuse.
93FirehawkTA
Jun 20 2013, 06:19 AM
Very nice!
SuperMacGuy
Jun 20 2013, 04:29 PM
OMFG. Thank you. Thank you so much. I am serious.
HoosierPE
Jun 21 2013, 03:32 AM
QUOTE (Steve91T @ Jun 19 2013, 03:38 PM)

I would buy one just to put in a display case. The most beautiful car part I think I've ever seen.
Maybe I missed it, or maybe you aren't announcing it yet, but any idea how much they will cost? I would assume with any race specific part, there won't be a warranty, right?
No, I haven't presented a cost as yet. I just received the volume quote from my machine shop last night while I was at the drag strip, and to my relief his cost was pretty much inline with my expectations. I've been working this afternoon on the complete Bill of Materials (BoM) so that I could completely understand my total cost for each assembly, and then I can set the price accordingly. I should have a price posted sometime tomorrow, and it should be in the ballpark of the MJM Racing re-manufactured parts from the 2010 time-frame, or in the $650ish each range, plus or minus a bit. I do get significant reductions in my machining cost at the 50 and 100 pc batch levels that can help bring the price down. (If you are really interested in purchasing a set, please let us know so we can get a head count for the first patch of parts.)
In regards to the warranty question, you are correct, no implied or explicit warranty due to the racing application. Of course, out of the desire to happy customers and good customer relations, we will deal with any issues that may arise in a professional manner and to the mutual satisfaction of both parties. Quite honestly, these things are way over designed. We considered smaller bearing sets, similar to the ones used in the older GM full size vans or pickup trucks, just to keep the cost down and the replacement parts readily available. These would likely have worked just fine, but we didn't want to any short cuts and want a part you could install and never worry about again, regardless of your use profile. We think we have hit that mark with our hub assembly. Our calculations were showing infinite life with very high G-loading (think soft compound 315s) and continuous high speeds. I'm going to send the bearing and loadings to Stan and let him run the calculations as a second opinion. Keep them greased and clean, and they should last the life of your car.
HoosierPE
Jun 21 2013, 03:37 AM
QUOTE (00 SS @ Jun 19 2013, 08:41 PM)

Nice job. The two piece spindle and flange seems like a good idea. I can't wait to see how it holds up to 315 and AX abuse.
We have several thousand commuting miles on the first set. Took them drag racing last night at 13.03 at 109mph. First auto-X is this Sunday and we will let everyone know how they are holding up.
HoosierPE
Jun 21 2013, 03:49 AM
QUOTE (SuperMacGuy @ Jun 20 2013, 12:29 PM)

OMFG. Thank you. Thank you so much. I am serious.
Your response made me laugh out loud and made my day. Thanks a bunch!
bigbegum
Jun 21 2013, 04:32 AM
Count me in on a set! Thanks!
JimMueller
Jun 21 2013, 04:17 PM
What type of recurring maintenance will they need and an estimate of how often for a street car running 315's?
HoosierPE
Jun 21 2013, 08:06 PM
QUOTE (JimMueller @ Jun 21 2013, 12:17 PM)

What type of recurring maintenance will they need and an estimate of how often for a street car running 315's?
Jim, if you are just running the car one street, then I would clean and repack them during your brake rotor and pad service, which depends greatly on your driving style. Otherwise, every 3 or four years, or ~30,000 miles or so. As long as the hub assembly is not leaking any grease and they are still tight, like with the OEM units, then everything should be OK.
If you auto-cross, then I'd look at them at least every two years. If you road-race, then they should be inspected every year.
Like most anything mechanical, the more detailed and frequent your service intervals, the longer the device will last.
HoosierPE
Jun 22 2013, 12:01 AM
Here are some photo's of the prototypes installed on the test vehicle.



Here's the old OEM part installed as a comparison.

A couple additional items that no one has brought up.
- This hub assembly is compatible with the one piece billet Track Brackets. Other brackets should work as long as their center clearance hole is of similar size as the knuckle.
- Right now, we do not have a source for the ABS sensor cap. We have searched high and low with no luck. We know they are being produced as all of the new replacement hubs come equipped with one. If anyone has any leads or contacts for a sensor cap source, please let us know. So for now, your will have to remove your old sensor cap and reuse it on the new hub. They clean up very well.
- For the ABS sensor cap, you will need the later plastic version and not the earlier metal sensor/dust cap. The earlier caps have tone rings with their teeth on the end face, while the later version's tone ring has radial teeth. The caps are not interchangeable, but surprisingly the ABS controllers seem to work with either version.
Pricing: The numbers are in and it looks like the list price needs to be $650 each, $1300 for the set. These will be complete assemblies, less the sensor cap, as shown in the earlier photos. We really want to order a batch of 50 hubs to get the better price break with the machine shop. So I'm trying find $20k to purchase all of the materials. As soon as I have that figured out, we will start taking orders.
93FirehawkTA
Jun 22 2013, 07:05 AM
Does your hub change wheel offset at all? Studying the various photographs, it looks as if wheels may be pushed out some? I ask because I'm running 18x11's with up to a 315 tire and my clearances to the fender are pretty tight as is.
Steve91T
Jun 22 2013, 01:35 PM
For CMC guys, pushing the wheels out some would be great.
tonycook
Jun 22 2013, 03:12 PM
I'm interested.
Are the wheels pushed out at all? I would think that would be ok with floating calipers(Stock or C5/6) but not fixed calipers(Stoptech)?
Thanks,
Tony Cook
HoosierPE
Jun 22 2013, 08:47 PM
The wheel mounting flange, where the rotor hat sits and then the wheel, is in the same location as the factory hub/bearing assembly, when measured from the knuckle mounting face to the outer face of the wheel mounting flange. We run 17x11s with 315s and we didn't want to mess up our current solution for making those fit in the front. We briefly considered makeing changes to eliminate the need for an 1/8th or 1/4" spacer, it's not possible within just the hub & bearing assembly, you'd have to modify the upright as well.
Here's a comparison picture of the mounting surfaces and offset:

If you think you see a difference, it's likely an illusion with a shinny new vs. crummy looking old part. Also, our housing diameter between the wheel flange and housing mounting flange is almost a half inch larger than the stock part to accommodate the larger tapered bearings. It is a direct replacement and your wheel/tire offset will be identical to how it was with your old bearings.
Also, just did a trial fit on a '91 C4 Corvette and they will bolt right up. I'll load some pictures later today. We may offer a version without the taped holes, but we need to see if we can get an Allen head cap screw to fit next to our larger housing diameter, it doesn't look like the factory C4 bolts will. If there is not enough room for the head to fit, then the C4 owners will need to run the bolts in from the back side and work out a different retention for the ABS wire bracket that uses the ends of the top two bolts.
Chevy053
Jun 23 2013, 12:42 AM
Very nice part.
Whats weight of one fully assembled?
I'm assuming the two piece spindle and flange are never intended to be separated (via a press) in case of service of failure?
HoosierPE
Jun 23 2013, 03:25 AM
QUOTE (Chevy053 @ Jun 22 2013, 08:42 PM)

Very nice part.
Whats weight of one fully assembled?
I'm assuming the two piece spindle and flange are never intended to be separated (via a press) in case of service of failure?
Thanks Chevy053. They turned out better than expected.
The stock part with studs weighs 8.3 lbs and the HPE part with the longer ARP studs weighs in at 10.2 lbs, or just under a two pound increase.
Our intent with the shrink fit was to make the joint permanent. We were able to disassemble our first sample when the pin didn't sit flat against the flange doe to a radius issue. Just for grins, we tried to press it out with my 10 Ton press. We maxed the press out and nothing happened. Just as we were about to release the pressure, the was a loud pop and the pin moved a little bit. We kept pound on the press with a hammer and the shock load helped jar the parts and we eventually got them separated. A shrink fit with the same interference as a press fit has over 3 times the retention force of a press fit which is why we selected this method. We fixed the radius issue and reassembled this unit without issue, but because it has been pressed apart and re-shrunk, I'm not sure I want to put it on a car. We will have to conduct some further testing to see if pin replace is possible without losing system integrity, but for now I would say that the pin and mounting flange are not serviceable separately.
jb442
Jun 23 2013, 08:15 AM
I'm interested. Please add me to the list.
tonycook
Jun 24 2013, 03:13 AM
Since the wheel mounting dimensions are the same, I'm very interested.
Thanks
Chevy053
Jun 24 2013, 11:56 AM
What was the reason for the design decision to go with a 2 piece flange. Was a single piece considered?
HoosierPE
Jun 24 2013, 02:02 PM
QUOTE (Chevy053 @ Jun 24 2013, 07:56 AM)

What was the reason for the design decision to go with a 2 piece flange. Was a single piece considered?
Primarily it was a cost & affordability thing, for material, machine time and tooling. Ideally, you'd like to have a one piece forging that is near the final shape and then machine that piece down to the final product. That is how the OEM pieces are done. No way to justify the forging tooling right now, which would probably be $10k or more, with what I believe will be low volumes (hundreds not thousands). We use pre-hard 4140 for both the pin and the flange which is a lot more costly than mild steel, and starting with a 6" diameter billet and whittling it down to 1" diameter in some spots generates quit a bit of waste.
At first we thought we would use a heavy press-fit and then I remembered shrink-fitting from my college days and started researching that process. The Machinery's Handbook goes through the process in great detail. The added bonus was the much higher retention force over a press-fit with the same amount of interference, 3.66 times for an axial pull and 3.2 times in torque or rotation. (This application doesn't see any rotational torque since it is not a driven axle.) An interesting side note; all of the train axles and wheels are a shrink-fit.
Turns out the two piece design might be the better performing design when you consider the stress concentrations and reverse bending cyclic loading of the application. On a one piece design, the transition from the flange to pin diameter becomes critical to avoid stress concentrations and a fatigue failure. If that radius or filet is too small, or there are surface imperfections, it becomes a stress riser and the focal point of crack initiation.
Update: We ran our first Auto-X on Sunday in my son's '95 LT1 (383) Camaro running 315 Khumo's. We had 6 runs on 65 second course with no change in preload on the prototype hubs.
SuperMacGuy
Jun 25 2013, 03:01 AM
I am all for anything that is stronger than the current design- in that I mean if the 2 piece design can be made to handle stress better then that is what I would want. I had 2 of the MJM hubs break on me (please see my long threads on it
elsewhere here) and the pieces that were used for the spindle weren't forged properly despite efforts to source the best possible blanks. It seems like the stresses can be high and heat treating is a sort of black-art/science. I'd much rather have a part that bends out of round and I have to replace it, than to have a full on failure (like I had at speed). The taper bearings are great, but, from my first hand experience, I want that spindle to be stronger than the Wrath of Zeus.
HoosierPE
Jun 25 2013, 04:03 AM
QUOTE (SuperMacGuy @ Jun 24 2013, 11:01 PM)

I am all for anything that is stronger than the current design- in that I mean if the 2 piece design can be made to handle stress better then that is what I would want. I had 2 of the MJM hubs break on me (please see my long threads on it
elsewhere here) and the pieces that were used for the spindle weren't forged properly despite efforts to source the best possible blanks. It seems like the stresses can be high and heat treating is a sort of black-art/science. I'd much rather have a part that bends out of round and I have to replace it, than to have a full on failure (like I had at speed). The taper bearings are great, but, from my first hand experience, I want that spindle to be stronger than the Wrath of Zeus.
Wow Chris, I just read about your escapades with the previous hubs. I'm glad it wasn't worse.
I had not read about these failures before we finished our design, but I sure was thinking about all of the possible failures during the design process. I'm glad we did a clean sheet approach for this new design as it removed many constraints or compromises in the design process. With a completely new housing, we were able to grow the size on everything; the bearings, the pin diameter (1.5" at the big bearing, 1.25" on the small end), and the pin and hub length for a wider bearing span. Unlike the one piece hubs (OEM or aftermarket) we don't have that high stress corner area in the flange to pin transition. All three major components are pre-hard 4140 that has been case induction hardened only in the pin area where the two inner bearing races rest and the step on the flange where the seal rides. We did pay for extra samples required for sectioning in setting up the hardening process. (I'm keeping these samples and reports indefinitely...) The 4140 material is billet, which removes the bad casting or forging issues.
I talked with my machine shop this afternoon and we are ready to kick off a 100 piece batch of these things. I believe we have covered all of the questions posted on the design. If anyone sees any glaring issues, please let us know as there is time for a few changes. Parts should be available before the end of July. I've started a list, so if you are
sincerely interested in a set, please let me know. Price is $650 each, $1300 for a set of two. (Right now, we have not located a source for the ABS sensor cap, so you will need to reuse the ones from your old bearings.)
BTW, we did a trial fit on a '91 C4 Corvette. They bolt right up, just need to run the OEM fasteners in from the back side and discard the nuts.
MarkT
Jun 25 2013, 05:04 PM
It's not that critical of a question (or issue for that matter) but can they be set up for screw in wheel studs? I went with 1/2" screw in ones on my Strange axle shafts and would at least like to get back to the same lug nut all around
HoosierPE
Jun 25 2013, 05:53 PM
QUOTE (MarkT @ Jun 25 2013, 01:04 PM)

It's not that critical of a question (or issue for that matter) but can they be set up for screw in wheel studs? I went with 1/2" screw in ones on my Strange axle shafts and would at least like to get back to the same lug nut all around

We might be able to do something special for you. Send me the info on what thread you need in the flange and I'll talk to our shop and let you know.
00 SS
Jun 25 2013, 11:54 PM
FYI, if you can get the flange holes threaded, Turner motorsports sells a threaded stud that's reasonably equivalent to the ARP studs in length and size.
SSTAT
Jun 26 2013, 01:17 AM
Jut this spring I officially depleted every junk yard I know of these hubs. I definitely want some (NEED some) but not with only some daily driving and one autocross worth of testing on them. There were high hopes for costly past designs that failed. I will shell out $1300 but only after someone has a season or so of actual racing on them and makes sure the wheels don't fall off. From a marketing standpoint wouldnt it make sense to get some real world (ie. not just one autocross) racing data before presenting these to the 4th gen/C4 crowd? Street cars don't need these.
93FirehawkTA
Jun 26 2013, 02:28 PM
Very interested. Thanks.
FASTFATBOY
Jun 26 2013, 09:02 PM
In for pricing and durability testing.
I want to know if they will handle a set of 315 NT-01's on a 3800 lb car on track.
Chevy053
Jun 27 2013, 03:06 AM
QUOTE (HoosierPE @ Jun 24 2013, 10:02 AM)

QUOTE (Chevy053 @ Jun 24 2013, 07:56 AM)

What was the reason for the design decision to go with a 2 piece flange. Was a single piece considered?
Turns out the two piece design might be the better performing design when you consider the stress concentrations and reverse bending cyclic loading of the application. On a one piece design, the transition from the flange to pin diameter becomes critical to avoid stress concentrations and a fatigue failure. If that radius or filet is too small, or there are surface imperfections, it becomes a stress riser and the focal point of crack initiation.
Thats what I was getting at. Was just curious if that was by accident or not.
HoosierPE
Jun 27 2013, 06:35 AM
QUOTE (SSTAT @ Jun 25 2013, 09:17 PM)

Jut this spring I officially depleted every junk yard I know of these hubs. I definitely want some (NEED some) but not with only some daily driving and one autocross worth of testing on them. There were high hopes for costly past designs that failed. I will shell out $1300 but only after someone has a season or so of actual racing on them and makes sure the wheels don't fall off. From a marketing standpoint wouldnt it make sense to get some real world (ie. not just one autocross) racing data before presenting these to the 4th gen/C4 crowd? Street cars don't need these.
SSTAT,
That's one view point, but as you pointed out, the supply of seasoned salvage yard parts are drying up and we all know the parts store replaces don't last like they should. I understand the community has been burned by past attempts, and that is exactly why I created the parts shown here. I studied all of the previous attempts and their short comings and also the original part design and improved on every aspect of these other designs. In a perfect world, with nothing but time, yes, it would be great to wait until we had a season or two exposure on these before we offer them up, but I believe the need far out ways the risk at this point. If, in my professional engineering assessment I thought there was any possibility of catastrophic failure, I would not have offered them up to this forum in the first place. If the improvements are not apparent to you in the pictures and descriptions above, then you should probably wait until next year.
camarokid91
Jun 27 2013, 05:06 PM
Any thoughts on these being ESP legal ?
Chevy053
Jun 27 2013, 07:16 PM
QUOTE (camarokid91 @ Jun 27 2013, 01:06 PM)

Any thoughts on these being ESP legal ?
We never got a straight 100% answer on the design in
THIS THREAD.
This design is similar so I wouldn't expect much of a different result. If anything these might be less legal (or more illegal). The other design re-used the original hub base which made them visually more similar to a stock replacement hub.
SuperMacGuy
Jun 28 2013, 12:26 AM
I'm not on the SEB, but my opinion is that, locally/regionally, no one would have a problem if I used them. In fact no one would ever notice, nor care, I bet. Nationally, maybe there is a question, but this could be viewed as a direct replacement part for worn out parts. There's not an allowance in the rulebook for "more well designed replacement hub". Then again, there's no mention of replacement of mundane items like fuel filters, valve stems, oil filters, or rear axle bearings. It's just assumed no one cares nor it makes any difference.
There is no performance advantage gained. In fact, the additional weight could be viewed as a weight penalty. Or, you could argue it is a safety improvement, as there is less chance of pad knockback from worn hubs and thus less chance of losing braking ability. Could you claim you bought them as direct replacements and didn't know the differences internally? If it were sold at AutoZone in a black box with a rusty patina on them, would anyone know the difference?
Anyone who would argue this is any type of actual on-track performance advantage would need their decision making authority revoked.
I think the previous SEB "no comment" (other thread) was sort of saying, "it's not a big deal and it would be too restrictive to put an actual ruling/wording on them. run them as is, and don't worry about protests". Wasn't Sam on the committee back then? I hope he would have said these would be OK to use.
SSTAT
Jun 29 2013, 02:05 AM
QUOTE (HoosierPE @ Jun 27 2013, 02:35 AM)

QUOTE (SSTAT @ Jun 25 2013, 09:17 PM)

Jut this spring I officially depleted every junk yard I know of these hubs. I definitely want some (NEED some) but not with only some daily driving and one autocross worth of testing on them. There were high hopes for costly past designs that failed. I will shell out $1300 but only after someone has a season or so of actual racing on them and makes sure the wheels don't fall off. From a marketing standpoint wouldnt it make sense to get some real world (ie. not just one autocross) racing data before presenting these to the 4th gen/C4 crowd? Street cars don't need these.
SSTAT,
That's one view point, but as you pointed out, the supply of seasoned salvage yard parts are drying up and we all know the parts store replaces don't last like they should. I understand the community has been burned by past attempts, and that is exactly why I created the parts shown here. I studied all of the previous attempts and their short comings and also the original part design and improved on every aspect of these other designs. In a perfect world, with nothing but time, yes, it would be great to wait until we had a season or two exposure on these before we offer them up, but I believe the need far out ways the risk at this point. If, in my professional engineering assessment I thought there was any possibility of catastrophic failure, I would not have offered them up to this forum in the first place. If the improvements are not apparent to you in the pictures and descriptions above, then you should probably wait until next year.
Fair enough, but I think the other designs were by engineers also, and had more than one event on them before they failed. Nothing in those pics is apparent to me as I'm not an engineer, but I thought professional engineering assessments generally included testing (in the target environment). I truly do have the highest hopes for you and your design.
mr.beachcomber
Jun 29 2013, 05:59 PM
QUOTE (SSTAT @ Jun 29 2013, 02:05 AM)

...I think the other designs were by engineers also..
I think that the original design was more than adequate for the task at hand. (After all, GM had to take into consideration that their product would be raced, auto-xed, and subjected to more stress and strain than simple straight-line driving.)
Just wanted to point out that even though the OEM and aftermarket designs were developed by professional engineers, there is a world of difference between a product whose price is controlled by bean counters looking to maximize profit and a product designed/manufactured by someone concerned more about quality, e.g., tolerances, use of higher quality steel, racing quality studs, etc.
A case in point: Years ago, Chicago Rawhide used to supply the best C4 wheel hub assemblies until a bean counter sent their operation off shore to maximize profits. Now you get the luck of the draw. I have seen new hub assemblies that had as much or more play than the worn assemblies they were meant to replace.
Personally, I would rather have a product like that offered by Hoosier Engineering than a bucket full of Chicago Rawhide hub assemblies that I have to test to find the best units.
93FirehawkTA
Jul 3 2013, 01:34 AM
QUOTE (mr.beachcomber @ Jun 29 2013, 01:59 PM)

After all, GM had to take into consideration that their product would be raced, auto-xed, and subjected to more stress and strain than simple straight-line driving.
I would say exactly the opposite. I think all GM designed 4th gen f-bodies for was "Friday night drags". All the money was in the drivetrain.
HoosierPE
Jul 4 2013, 04:27 AM
Hey guys. Sorry I've been out of touch recently. Traveled to Oregon and Texas last week and getting caught up on somethings this week, now the 4th is here. I wanted to let you know that I ordered 100 assembles from our machine shop last Friday (will make 50 pairs of hubs). They have promised to have them machined and plated by the end of the first week of August. So we should be shipping assemblies by the second week of August. We will be setting up a PayPal account for the business in the next couple of weeks and will accept orders at the end of July.
SSTAT, I just wanted to let you know that you are correct; in a perfect world, you would perform extensive laboratory and vehicle durability testing to prove out any new design. When you can spread this cost over a 100,000 or 1 million of something, it really becomes a non issue. If you have to spread this extensive cost out over several 100 assemblies, it really is cost prohibited. It could easily add $1000 to every assembly at such low volumes. So our approach was to over-design this assembly to the greatest extent possible. We have the largest tapered bearings that can physically be packaged in this design space and still fit the stock upright/knuckle. The tapered roller bearings out perform ball bearings in every category.
Relative to the legality of these hub assemblies, it was covered in the other thread referenced above, and they didn't receive a final ruling from the SEB. I for one, will be running these in all four of our 4th Gens and hope to take one or two of them to the Solo Nationals. I would think you could argue a performance disadvantage with the nearly four lbs added to the front of the car.
shortbus
Jul 9 2013, 01:08 PM
I am in. I will PM with my best contact info.
Thank you.
GNC Rick
Aug 19 2013, 08:38 AM
Have these started shipping ? They look awesome & looking forward to some feedback from members here after they get them or try them out.
FASTFATBOY
Aug 19 2013, 12:08 PM
Did firm pricing ever come out?
93FirehawkTA
Aug 24 2013, 01:26 AM
QUOTE (HoosierPE @ Jul 4 2013, 12:27 AM)

Hey guys. Sorry I've been out of touch recently. Traveled to Oregon and Texas last week and getting caught up on somethings this week, now the 4th is here. I wanted to let you know that I ordered 100 assembles from our machine shop last Friday (will make 50 pairs of hubs). They have promised to have them machined and plated by the end of the first week of August. So we should be shipping assemblies by the second week of August. We will be setting up a PayPal account for the business in the next couple of weeks and will accept orders at the end of July.
John,
Please update us on your production status.
Thanks,
Ilario
HoosierPE
Aug 24 2013, 09:10 PM
Hey Guys, sorry I haven't been keeping up with the posting. It's been a rough 3 or 4 weeks that started with a kidney stone and surgery 4 days later (wasn't on my bucket list and don't ever want one again), followed up with the passing of my father and we just admitted my mother to the hospital this week. When my luck breaks, I'm going to buy a bunch of lottery tickets...

Sorry, back to the front hubs. I put a hold on the model shop order mid-July, just before they ordered all of the material. A few questions came up relative to heat treatment on the spindle/pin that I wanted to follow up on. Basically trying to dot all of our I's and cross all of our T's to make sure these things are absolutely bullet proof. We consulted with two more materials experts to get their input and feel we have covered everything. We kicked the machine shop back off last week and the raw materials arrived this week on Thursday. (I'll try to post a picture of all the material for 100 assemblies, its a lot of steel.)
The spindle will still be made from the 4140 material, but will received a full heat treat and then case hardening to achieve the desired fatigue strength. For ease of assembly and maintenance, we left a small slip-fit between the spindle and the inner race of the bearings. Timken's design manual does recommend a press-fit designs with rotating spindle shafts, which ours is, but we thought we would give it a try first with the slip-fit. With the slip-fit, the bearings were walking around the shaft a bit and showing some signs of wear. We have updated the design per the Timken recommendations and the bearings will now be pressed onto the spindle, similar to the pinion shafts in many differentials. We are also adding a solid spacer with shims between the bearings' inner races to further enhance the design and lock all the parts in place. Placing the spindle in tension with the use of the bearing spacer will also enhance the fatigue strength of the assembly.
The shop will start on the parts next week and we should have them back to us around the 3rd week of September. Assembly and shipping should take place the last week of September. I will post specifics for ordering in a few weeks. Pricing is $650 each, $1300 for set of two.
93FirehawkTA
Aug 25 2013, 05:35 PM
Very sorry for your loss and troubles John. I've been in similar circumstances. Take care of yourself and family and when convenient let us know when/how to order.
StanIROCZ
Sep 7 2013, 01:20 AM
John sent me some of the design details of this hub unit so I could do a bearing life analysis.
I started by creating a duty cycle. This duty cycle is far from being perfect or actual. It is very simplified estimation of the loading and cycles that this hub unit will see on a car. After creating the duty cycle I made some assumptions for the vehicle and started calculating the dynamic corner weights at each wheel and the braking and cornering forces at the contact patch. Then calculated the loads and moments along the shaft axis at the wheel center. Plugged that data along with the duration (cycles) at each load case into my bearing calculation software. Add up the damage at each load case to get the cumulative damage and calculate the reliability. I can go into more detail if necessary.
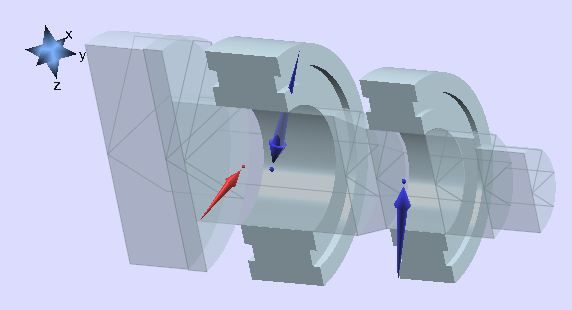
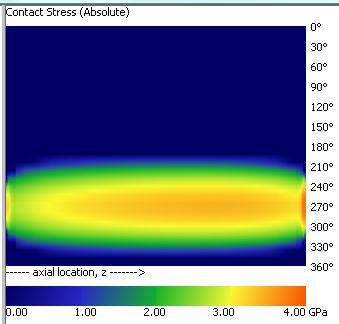
Inner bearing, roller contact stress, 1.25G trail braking
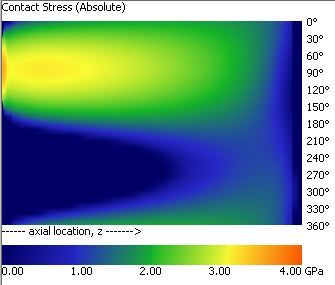
Outer Bearing, roller contact stress, 1.25G trail braking
The short story is the damage is low and as a result the reliability is high. As you could probably guess even without doing these calculations that putting larger taper roller bearings in place of smaller ball bearings is going to result in longer life.
The small text:
Many assumptions were made and there might be mistakes in the analysis. No warranty expressed or implied. Use at your own risk. yada yada
matt f
Oct 25 2013, 04:37 PM
While my car was up on jacks the other day, I noticed a little play in the front end. Seems like hubs.
How's this going?
HoosierPE
Oct 25 2013, 06:04 PM
Hey Matt,
The first 100 pieces are nearly completed at the machine shop. They got behind on my and it's cost us several weeks. The wheel mounting flanges and spindle pins are done and off to to be plated. The bearing housing is going through the final CNC milling process to square them off and add the tapped mounting holes. Unfortunately, I we are still a week or two away from final assembly.
I've been waiting to post anything until I knew for certain when I would have the parts in hand. As soon as I have all the parts in hand, hopefully by the end of next week, I will post the details for ordering sets of these. Right now, we will only be accepting credit cards purchases, but that may change in the future.
Thanks for the inquiry.
John
HoosierPE
Jan 18 2014, 05:56 PM
Happy New Year everyone!
Sorry I haven't provided any updates on the hub project in a while, but I've been wanting to wait until I had good news, like they are ready to ship. Unfortunately, that is not the case. We experienced lengthy delays in the machining, heat treat and plating process.

I do have all of the piece parts in hand for the 100 assemblies, but I'm very unhappy with the quality of the plating finished appearance.

It was very dull, blotchy and streaky, definitely not the appearance of a quality part. They may be going back to the plater to be stripped and replated with a different process. And this may add several weeks to the timeline.
One good piece of news; I did find a source for new ABS sensor caps. So the new hubs will ship with new ABS caps and will be ready to install, right out of the box. No need to remove and clean your old sensor cap.
Stay tuned, I'm hopeful that I'm a few weeks away from providing the good news.
John
trackbird
Jan 19 2014, 06:31 PM
Nice work John! The ABS caps will be a nice addition. Sorry about the plating work...I never liked dealing with that stuff when I was building and selling the brake conversion brackets (once upon a time). Sounds like there is light at the end of the tunnel. Glad you're nearing the end.
This is a "lo-fi" version of our main content. To view the full version with more information, formatting and images, please
click here.